O tratamento de rochas e solos para melhorar seu comportamento geotécnico, pode ser por meio de injeções de cimento, no qual consiste em fazer penetrar nos vazios do maciço natural (solo ou rocha) um produto líquido (geralmente nata de cimento) que tenha a propriedade de endurecer depois de certo tempo de aplicação.
Existem três tipos de injeções:
injeção de colagem
injeção de consolidação
injeção de impermeabilização / cortina de injeção
As injeções de colagem objetivam eliminar os vazios existentes entre o concreto e a rocha; as injeções de consolidação visam melhorar as condições de resistência da rocha de fundação, embora também tenham uma função secundária de impermeabilização; as cortinas de injeção têm como principal objetivo controlar a percolação da água através da fundação.
A eficiência de um tratamento de injeção depende, entre outros, dos seguintes fatores: planejamento da perfuração/injeção; tipo de calda; pressão de injeção; cuidados operacionais; e controle da eficiência.
Processo executivo de injeção
Em geral, a injeção é efetuada através de furos abertos, em sua maioria com equipamento roto-percussivo. Esta perfuração é executada com a circulação de água ou ar comprimido para se evitar a penetração de detritos nos vazios e limpeza do furo. O material escavado na perfuração vai sendo expulso do furo durante o processo de perfuração, por esta circulação de fluídos.
Estes detritos gerados na perfuração poderão causar a colmatação das fraturas, fissuras ou vazios, impedindo a entrada de calda de cimento, por isso devem ser retirados.
Para a execução das injeções é usual fazer uma linha de furos exploratórios. Nestes furos o processo de perfuração é rotativo com extração de testemunho e ensaios de perda d’água para que se conheça o grau de faturamento da rocha; a percolação de água; e estrutura de maciço. Esta análise será repetida após a execução das injeções para analise da eficácia do processo.
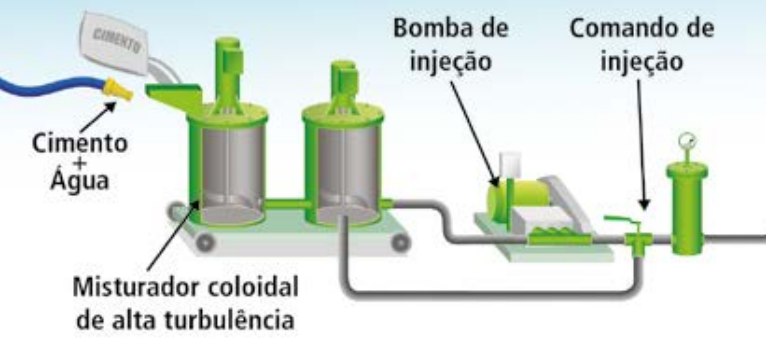
Equipamentos de injeção e sua organização
a) Misturadores: Preparam a calda, em geral de alta rotação para dispersar bem os grânulos de cimento;
b) Agitadores: Mantêm a calda homogênea e impede que a mesma se solidifique antes do tempo adequado;
Nota: Usualmente agitadores e misturadores estão acoplado, formando um só equipamento.
c) Bombas: Injetam a calda de cimento sob pressão. Devem ter capacidade de injetar grandes vazões à pressão bem elevadas;
d) Equipamentos Complementares: Mangueiras; engates rápidos, registros, manômetros, conjunto de hastes e obturador, que descem ao furo para efetuar a injeção em trechos mais profundos.
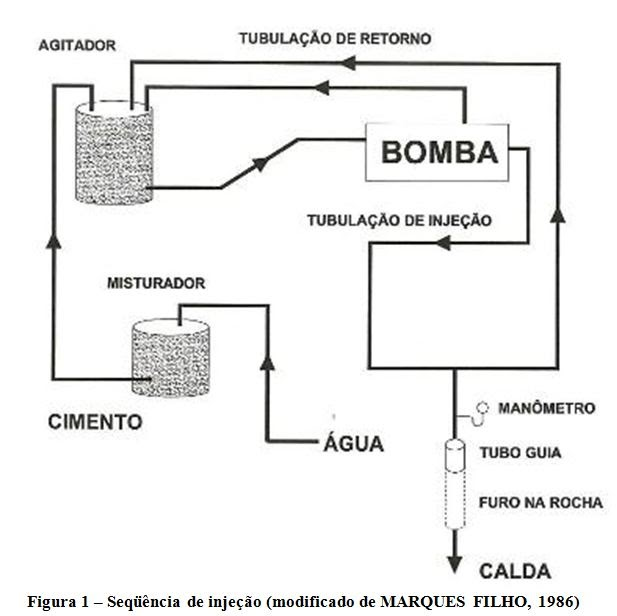
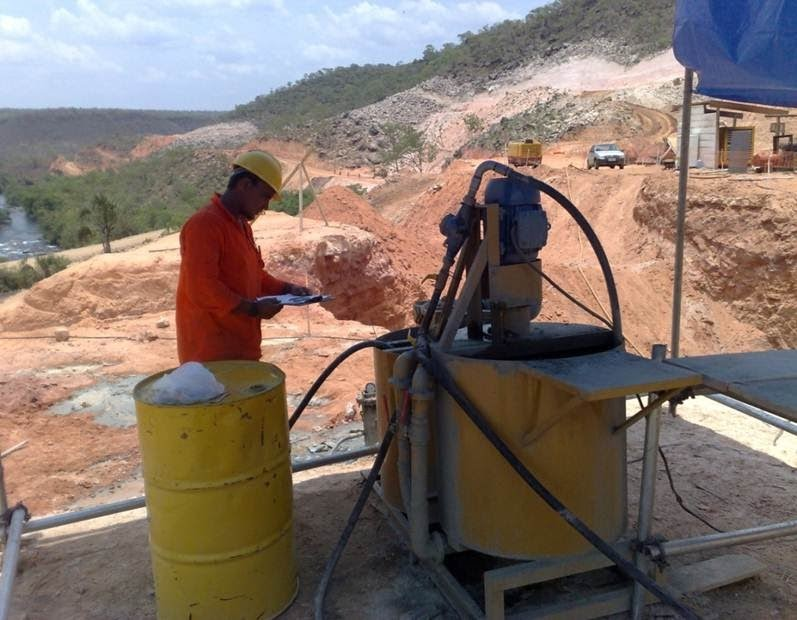
Agitador de calda e misturados duplo vertical, utilizados para injeção de calda de cimento em barragens
Método de execução
A Injeção de Cimento pode serguir dois métodos comuns de se utilizarem. O método Ascendete e o método Descentente, descritos a seguir:

Método ascendente
Nas injeções ascecendentes o furo é executado até a profundidade final e a injeção é feita com auxílio de um obturador, posicionando na extremidade superior de cada trecho a injetar.

Método descendente
Nas injeções descendentes o furo é executado até a profundidade do primeiro trecho de injeção, executando-se a injeção do trecho com o obturador posicionado no topo do trecho. Após a pega da calda, reperfura-se o furo no trecho injetado, prosseguindo com a perfuração até o final do segundo trecho de injeção, repetindo-se a seguir as operações até alcançar a profundidade final do ruro.
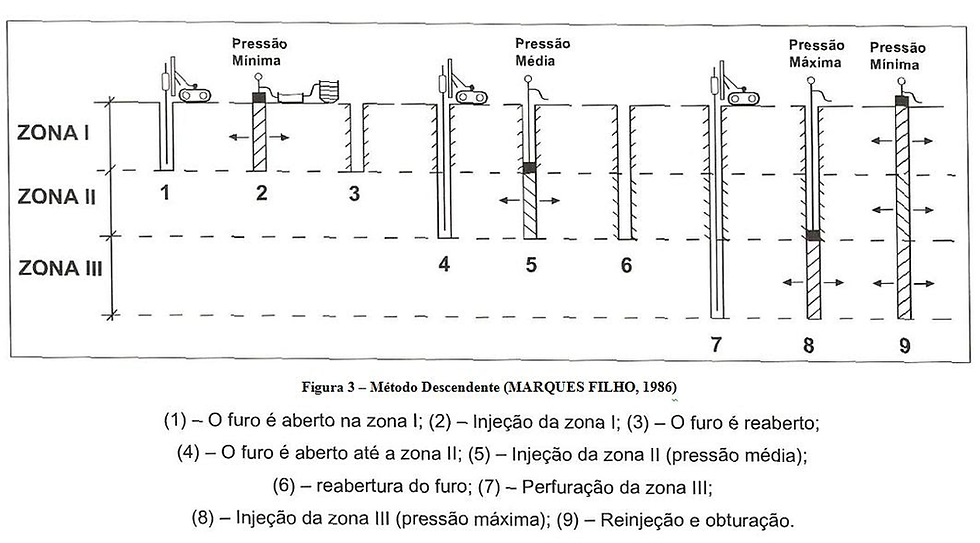
O método ascendente é mais rápido e de menor custo, sendo geralmente utilizado, entretanto, permite a comunicação da calda com os trechos superiores não injetados ou mesmo com a superfície. Em rchas muito fraturadas pode ser difícil a fixação do obturador, oque leva à utilização do método descendente nessa situação.
Tipo de calda e seu traço
As caldas de injeção usualmente empregadas são constituídas por uma mistura fluída de água e cimento, à qual podem ser adicionados bentonita, areia, pozolana e outros produtos. Outros tipos de caldas, como aquelas à base de compostos de silicatos e resinas são empregadas para injeção em solo, porém, seu uso é limitado, predominando amplamente as caldas de cimento.
A escolha do tipo de calda mais adequada depende de uma série de fatores, dentre eles a permeabilidade, conforme mostrado abaixo.

As caldas de água/cimento são geralmente definidas pela proporção água/sólidos, cujos valores mais usuais stuam-se entre 1:1 a 0,5:1. A proporção de água determina a viscosidade e a fluidez da calda, sendo responsável pela sua injetabilidade, ou seja, sua capacidade de ser bombeada e penetrar nos vazios do maciço. A areia é adicionada às caldas de água/cimento quando os vazios a serem preenchidos são maiores. A bentonita é utilizada para melhorar a injetabilidade da calda e a pozolana para substituir parte do cimento, reduzindo o custo da calda.
Por outro lado, como a calda deve ser capaz de penetrar no vazio a ser obturado, a granulometria da fração sólida da calda deve ser inferior ao tamanho dos vazios. Assim, a permeabilidade não necessáriamente reflete a injetabilidade do maciço, uma vez que altas permeabilidades podem ser devidas, por exemplo, a poucos vazios de grande abertura ou a muitos vazios de pequena abertura, servindo os dados da figura 22.8 apenas como orientação geral.
Com caldas à base de água/cimento, fraturas com abertura abaixo de 0,1 mm não são injetáveis, devido ao tamanho mínimo das particuls de cimento. A estabilidade da calda, ou seja, o tempo para que ocorra a sedimentação da fase sólida da calda, também é importante para a injeção. Caldas de baixa estabilidade podem provocar a obstrução prematura dos vazios devido à rápida separação das faes da calda.
As propriedades de viscosidade, fluidez, tixotropia e sedimentação das caldas são chamadas de características reológicas das caldas. Juntamente com a granulometria da fração sólida, essas propriedades são resonsáveis pelas características de injetabilidade das caldas. Assim, a escolha da calda depende de um conhecimento adequad das características dos vazios a serem obturados e das propriedades reológicas dos vários tipos de caldas passíveis de utilização. Outras características essenciais de uma calda são o tempo de cura ou de pega e, depois de seu endurecimento, a resistência mecânica, a permeabilidade e a durabilidade.
Em obras de grande porte, como numa barragem, onde os volumes de injeção são apreciáveis, são estudados diversos tipos de caldas à base de água/cmento, variando-se a relação água/sólidos e determinando-se suas características reológicas em laboratório. Esses estudos são completados por ensaios in situ, cujos resultados são avaliados por ensaios de perda d´água sob pressão, efetuados em perfurações feitas antes e depois das injeções, de forma a permetir a escolha da calda de injeção mais apropriada em função do custo e da eficiência.

Os aditivos e materiais mais comuns usados nas caldas seguem listados:
a) Micro-cimento: Trata-se de um produto cimentício a base de clínquer, micro pulverizado. Onde o diâmetro varia de 20 µm a 30 µm, possibilitando uma alta injetabilidade em micro-fissuras.
b) Bentonita: Utilizada geralmente em porcentagens muito pequenas (2 a 3% em peso dos sólidos) para melhorar a injetabilidade. A Bentonita, sendo uma argila altamente expansiva e tixotrópica, possibilita a diminuição do fator A/C da calda, reduzindo a massa especifica, seu consumo de cimento e fluidez da calda.
c) Tenso-Ativos: Substância que diminuem a tensão superficial e permite a perfeita “molhagem” dos grãos do cimento, melhorando a curva de injetabilidade.
d) Aceleradores: São empregados em injeções de maciços rochosos, quando se desejam obter resistências mecânicas relativamente altas as primeiras idades (economia de tempo). Os aceleradores mais empregados são à base de cloreto de cálcio, carbonetos e hidróxidos alcalinos e trietamolamina.
e) Expansores: aumentam a penetração e a estabilidade das caldas nas fissuras. O expansor mais comum e utilizado nas injeções de calda de cimento é o pó de alumínio.
Alem destes aditivos, são também utilizadas caldas com pozolana oferecendo as vantagens de maiores resistências a dissolução, menor permeabilidade e maior economia, mas com o inconveniente de ligeira diminuição da resistência a compressão.
OBS: é preciso verificar se a calda endurecida nas fissuras não terá menor resistência do que a própria rocha, o que tornaria ineficiente o acréscimo de qualquer aditivo.
Pressão de Injeção
As pressões de injeção constituem um parâmetro controverso e que deve ser bem estudado antes do inicio dos trabalhos, de modo a se obter os melhores resultados pelo menor custo. Uma maior pressão de injeção faz crescer a quantidade de calda injetada e sendo a pressão muito alta, pode determinar a perda de coesão da rocha/solo (craqueamento do solo).
A pressão ideal de injeção, para um determinado maciço rochoso de fundação, é a pressão máxima que não cause movimentação do maciço e, portanto é determinada em função da profundidade da zona injetada, estrutura da rocha, altitude das fraturas e da sobrecarga devida à estrutura e do nível do lençol freático.
As altas pressões geralmente trazem economia aos trabalhos, uma vez que elas tendem a produzir um alargamento nas fissuras e com isso permitem uma penetração melhor até mesmo de calda relativamente grossas e feitas com cimentos comuns. Também ampliam substancialmente a distância de penetração das caldas. Assim, pressões elevadas tendem a aumentar a quantidade de calda que é injetada a partir de um mesmo furo, aumentando seu raio de influência, fazendo com que se possa efetuar o tratamento de modo mais eficiente e com menor numero de perfurações. Como o custo da perfuração constitui, via de regra, a maior parcela no custo total de um trabalho de injeção, o emprego de altas pressões pode diminuir consideravelmente o custo de um tratamento deste tipo além de normalmente melhorar bastante a sua qualidade.
O principal argumento contra pressões muito elevadas é de que as mesmas podem causar danos irreversíveis à rocha como abertura de novas fraturas e até mesmo aberturas de juntas que estavam seladas no caso de rocha de baixa resistência.
O critério geralmente adotado consiste na aplicação de m presão máxima de injeção inferior ao peso da rocha sobrejacente ao trecho injetado, oque equivale à adoção de uma pressão de 0,25kgf/cm² por metro de profundidade. Este valor deve ser reduzido no caso de encostas onde a cobertura rochosa lateral é inferior àquela encontrada verticalmente ou quando a densidade da rocha for inferior a 2.500 kg/m³ (2,5 g/m³). Quando o fluxo de calda é pequeno, devido à pequena abertura das descontinuidades, a pressão da calda no interior da fratura será rapidamente equalizada, permitindo a utilização de pressões de injeção mais altas.
Num processo de injeção com vazão constante ocorre, na maioria das vezes, um comportamento de pressões semelhantes ao mostrado no gráfico abaixo, figuras 12 e 13, de onde pode ser ressaltado:
• Após abertura da manchete e rompimento da bainha (Pa), observa-se uma queda brusca da pressão (Pi), caracterizando o início da injeção no solo.
• À medida que a injeção prossegue, novos trechos do solo podem ser rompidos e preenchidos com material injetado, acarretando em aumento lento


Critérios de recusa ("nega")
Os critérios de recusa de calda, ou seja, o momento em que o bombeamento de calda é interrompido, paralisando a injeção ou substituindo a calda em uso, são fixados em função da extensão a ser tratada, das características reológicas da calda e da quantidade de calda já injetada. Para efeitos práticos, o critério de recusa é fixado pelo peso máximo de sólidos absorvidos por metro em cada trecho de injeção, conforme o exemplo da tabela a seguir, adotado em barragens de concreto sobre rochas duras. Atingida a absorção indicada, em quilos de sólidos da calda por metro de furo injetado, passa-se a injetar a calda da linha imediatamente abaixo, sendo que a calda 1:1:1 refere-se à água/cimento/areia, sendo chamada de argamassa. A rejeição orresponde ao retorno, pela boca do furo, durante 10 minutos, da calda bombeada à pressão máxima do equipamento de injeção.

Equipe de trabalho
Encarregado geral de serviços
a) Verifica: condições para entrada e movimentação de equipamentos no canteiro da obra; descarregamento de equipamentos, utensílios e ferramentas; instalação da central de injeção e implantação geral da obra.
b) Verifica programação de execução (sequência executiva) de acordo com
características da obra e necessidades do cliente.
c) Coordena o DDS (diálogo diário de segurança) antes do início das atividades de cada dia e instrui em relação à segurança durante a execução dos serviços.
d) Coordena locação, verticalidade e instalação do equipamento de perfuração, misturador e bomba de injeção de solo-cimento.
e) Orienta em relação aos procedimentos de perfuração, instalação do tubo de injeção e inspeção.
Operador de perfuratriz
a) Movimenta o equipamento de acordo com a sequência executiva.
b) Instala o equipamento no furo, observando locação e inclinação.
c) Verifica quantidade e tamanho dos tubos de revestimento colocados, para
que acompanhem a profundidade dos furos.
d) Detecta mudanças de camadas do solo à medida que a perfuração avança.
e) Detecta eventuais perdas d’água durante a perfuração.
f) Elabora registro dos dados de perfuração para inclusão no boletim.
g) Orienta auxiliares de perfuração quanto à utilização do ferramental necessário.
h) Instala o tubo de injeção no furo.
Injetador
a) Prepara o material a ser injetado.
b) Coordena a injeção, tanto no posicionamento do obturador quanto na injeção, de forma a atender as condições do projeto e a lavagem (pós-injeção) do tubo com válvulas-manchete.
c) Lança nos boletins os valores de pressão e volume injetados.
Auxiliar geral
Auxilia os especialistas nas atividades principais.
Comments